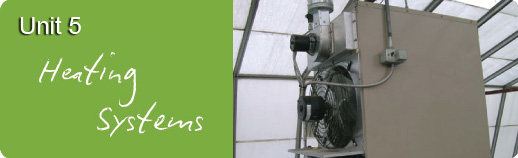
Section 3: Heat Distribution for Improving Temperature Uniformity
After heat is generated, it must be distributed throughout the greenhouse facility. Enough Btu must be provided to the greenhouse atmosphere (typically denoted as Btu/hr) to replace the Btu being lost from the greenhouse (to maintain a constant temperature but more Btu to increase temperature). Uniform distribution of heat energy, without having cold or hot spots in the greenhouse, is a very important but sometimes neglected aspect of greenhouse heating. Uneven temperatures can result in uneven crop growth rates, variation in maturation times, and can affect substrate drying rates.
When a central heating system is used to produce hot water or steam, a system of pipes is used to distribute the heat energy throughout the greenhouse. Pipes may be made of cast iron, aluminum or copper. Hot water is usually supplied to the greenhouse at 180° F or 203° F if it is pressurized. Steam is usually supplied at 215° F. Because less resistance occurs in moving steam, smaller diameter pipes can be used for steam as compared to hot water. Also, because steam is delivered at a higher temperature, it provides more Btu than hot water per linear foot of pipe. Therefore, fewer pipes (less linear feet) are needed when using steam. Enough linear feet of pipe must be placed in the greenhouse to allow for enough Btu/hr to be given off to adequately maintain temperature. The required length of pipe is then distributed throughout the greenhouse structure; typically along walls and under benches if they are present. The length of pipe required will depend on the Btu/hr required and the type of pipe used to distribute the heat energy. For example, if it is determined that a greenhouse structure requires 1,000,000 Btu/hr and 1.50 inch pipe is being used to distribute steam, 4762 ft of pipe (1,000,000 Btu/210 Btu per hr per ft) must be used in the greenhouse. This is the minimum total length of pipe that must occur through the greenhouse and the steam should move through this piping before exiting the greenhouse.
Stacked pipes (placed in layers along walls) are less efficient than single pipes. If pipes are stacked, additional pipes will be required to compensate for the reduced efficiency. As is demonstrated in the table below, the higher the temperature of the pipe or the greater the diameter of the pipe, the greater the number of Btu given off per linear foot of pipe. Finned pipes are more efficient at heat transfer than smooth pipes due to their increased surface area. Finned pipes may transfer four or more times the amount of heat as a smooth pipe. The advantage of finned pipes is that less pipe is required. The disadvantage of finned pipes is that they release more intense amounts of heat in a small area which can create hot spots.
Heat Available From Different Pipe Sizes Using Steam and Hot Water at Different Temperaturesz |
||
Heat Source |
Pipe Diameter |
Btu/hr/ft |
Steam at 215° F |
1.50 inch |
210 |
Steam at 215° F |
1.25 inch |
180 |
Hot water at 180° F |
2.00 inch |
160 |
Hot water at 203° F |
2.00 inch |
200 |
z Assumes a 60° F inside greenhouse air temperature. |
The first approach to creating uniform temperature throughout the greenhouse is pipe placement. The required length of pipe should be distributed throughout the greenhouse along the walls and under the greenhouse benches.
If a central heating system is used and the pipes placed along the lower walls and under greenhouse benches, the warm air rises, and as it does, it cools. This creates temperature stratification. Cool air in the gable area of the greenhouse descends down the inside walls of the greenhouse and creates cold pockets along the greenhouse walls. Horizontal airflow fans (HAF), placed below the gable and along the length of the greenhouse and in opposing positions to create a circular air flow pattern, create a horizontal air circulation pattern and force warm air to move down the length of the greenhouse and prevent temperature stratification.
When unit heaters are used, heated air is directly discharged into the greenhouse. The primary concern then becomes one of evenly distributing the heated air. If unit heaters are used to heat greenhouses, a temperature gradient can occur along the length of the greenhouse. Temperatures will be warmer closer to the unit heater. Several strategies can be employed to minimize the temperature gradient along the length of the greenhouse. The first is to use multiple unit heaters placed at opposite ends of the greenhouse in opposed positions. In addition to providing heat at both ends of the greenhouse, the opposed airflow assists with mixing of the greenhouse air and improves temperature uniformity. Where relatively long greenhouses are used, HAF fans may also be added to help move warm air down the length of the greenhouse and to further promote the mixing of air. In some cases, the unit heater may be connected to a polyethylene jet tube. The warm air is first forced down the length of the jet tube. After the jet tube fills, the warm air evacuates the tube from holes along its side. Jet tubes may also be used in combination with HAF fans.
Often in spring and fall, heating is required at night and cooling required during the day due to solar heating. The fan of the unit heater and polyethylene tube can be used (with fire box and fuel source turned off) for cooling in these situations if outside louvers are included. The louvers located behind the unit heater are opened and the fan turned on so that cool outside air is forced into the polyethylene tube. Additionally, the louvers can be closed and the fan turned on to improve internal greenhouse air circulation.
Some specialized heating systems use polypropylene or rubber tubes to circulate hot water in close proximity to the root system of the plants. There are many variations to this system, but the most common is the Biotherm® system. This system is most commonly used for increasing substrate temperature during propagation rather than general greenhouse heating.