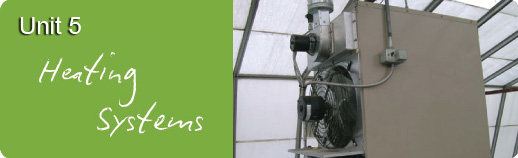
Section 5: Calculating Greenhouse Heat Requirements
In most cases greenhouse managers will not need to determine greenhouse heating requirements. In most cases greenhouses are custom designed or predesigned greenhouses are purchased. The greenhouse design and construction company will have determined heating requirements for the specific greenhouse for different locations and environmental conditions. However, it is useful to have a basic understanding of how greenhouse heating requirements are determined.
The underlying principle for determining the heating requirement of a greenhouse is to replace the Btu that are lost from the structure (Btu/hr) so as to maintain the temperature within a desired range. Typically, heat loss through radiation is ignored since the amount is negligible. Therefore, only heat loss through conduction and infiltration/exfiltration are usually determined. These losses are determined for the coldest expected temperatures occurring at night. These provide maximum values for the heating capacity that should be required during the coldest time of the year. During the day when solar input provides additional heat energy or during warmer times of the year, the full heating capacity may not be utilized. It is also common to actually install a somewhat higher heating capacity than required to provide some level of “insurance” heating capacity.
An example heating capacity example follows. There are different variations to these calculations, but the example below is typical and provides an examples of the factors considered when determining required heating capacity.
ht = hc + hsa
where:
ht = total heat loss from greenhouse
hc = heat loss by conduction
hsa = sensible heat loss by mass transfer
hc = AU(ti-to)W
where:
hc = heat loss by conduction
A = surface area
U = heat transfer coefficient (to be taken from table of standard values below)
ti = desired inside air temperature
to = minimum outside air temperature
W = wind correction factor
hsa = 0.02(ti-to)(V)(M)(W)
where:
hsa = sensible heat loss by mass transfer
ti = desired inside air temperature
to = minimum outside air temperature
V = greenhouse volume (to be calculated)
M = air exchanges per hour (value taken from table of standard values below)
W = wind correction factor (value taken from table of standard values below)
Heat Transfer Coefficient for Various Glazings and Surfaces (U) |
|
Surface |
Btu/ft2/hr/oF difference |
Glass, single layer |
1.13 |
Glass, double layer |
0.65 |
Polyethylene film, single layer |
1.15 |
Polyethylene film, double layer |
0.70 |
Fiberglass |
1.00 |
Bi-wall polycarbonate |
0.65 |
Bi-wall acrylic |
0.65 |
Concrete block, 8" |
0.51 |
Concrete block with foam urethane |
0.13 |
Poured concrete, 6" |
0.75 |
Air exchanges per hour for various greenhouse types (M) |
|
Greenhouse type |
Air exchanges per hour |
Metal greenhouse with glass |
1.08 |
Wood and steel greenhouse with glass |
1.05 |
Wood greenhouse with glass, tight |
1.00 |
Wood greenhouse with glass, moderately tight |
1.13 |
Wood greenhouse with glass, loose |
1.25 |
Wood greenhouse with FRP |
0.95 |
Metal greenhouse with FRP |
1.00 |
Metal greenhouse with double glass |
0.70 |
Metal greenhouse with single layer of polyethylene |
1.00 |
Metal greenhouse with double layer of polyethylene |
0.70 |
Correction factors for wind speed (W) |
|
Wind speed (mph) |
Correction factor |
less than or equal to 15 |
1.00 |
20 |
1.04 |
25 |
1.08 |
30 |
1.12 |
35 |
1.16 |
As an example, the Btu requirement of an A-frame greenhouse is determined below. The greenhouse is a 40 ft x 100 ft, glass-glazed, metal frame greenhouse, and of tight construction. The gable is 8 ft from the eave to the peak. It has an 8 ft wall with 2 ft of the wall being a 6-inch concrete block curtain wall. The maximum expected wind velocity is 15 mph. The minimum expected low temperature is 0oF, and the minimum desirable inside temperature is 60° F.
The surface area glazed with glass is 8000 ft2, and the surface area for the curtain wall is 560 ft2.
The volume of the structure is 48,000 ft3.
Therefore:
hc = 8000(1.13)(60)(1.0) + 560(0.51)(60)(1.0) = 559,536 Btu/hr
hsa = 0.02(60)(48,000)(1.08)(1.0) = 62,208 Btu/hr
ht = 559,536 Btu/hr + 62,208 Btu/hr = 621,744 Btu/hr
An example is outlined below for a 30 ft x 100 ft quonset greenhouse (covering is 47 ft wide), with a double polyethylene covering. The maximum expected wind velocity is 15 mph. The minimum expected low temperature is 0oF, and the minimum desirable inside temperature is 60° F.
The following equations can be used to estimate surface area and volumes of quonset greenhouses:
Circumference of a circle = 2πr
Area of a circle = πr2
Total surface area of a cylinder = (2πrH) + (2πr2)
Volume of a cylinder = πr2H
Therefore:
The surface area glazed with polyethylene film is 5409 ft2.
The volume of the structure is 35,325 ft3.
and:
hc = 5409(0.70)(60)(1.0) = 227,178 Btu/hr
hsa = 0.02(60)(35,325)(0.70)(1.0) = 29,673 Btu/hr
ht = 227,178 + 29,673 = 256,851 Btu/hr
As can be seen in these examples, the basic approach is to determine volume of surface area and volume of the structure. The Btu/hr requirement for a standard structure is then corrected for those variables that increase (greater temperature differentials, higher wind speeds, higher U values for glazing, poorly built or older or poorly structure) or decrease the rate of heat loss. These example calculations also demonstrate the large number of Btu/hr heating capacity that may be required. Small greenhouses such as those demonstrated in these equations required hundreds of thousands of Btu/hr. A large greenhouse or greenhouse complex will usually require millions of Btu/hr.