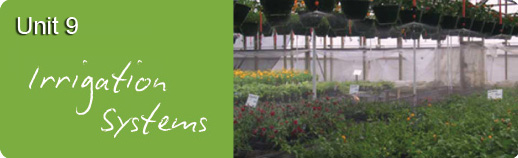
Section 5: Common Supporting Components of Irrigation Systems
Injectors
Fertilizer injectors are a critical component of irrigation/fertilization systems as they are used to blend a concentrated fertilizer stock solution with water to deliver a fertilizer solution of the desired concentration to the crop. If concentrated stock solutions and injectors are not used, extremely large volumes of the final fertilizer solution (a thus very large storage tanks) will need to be prepared (such as are needed with ebb-and-flow benches, troughs, and flood floors). Fertilizer injectors may be purchased that blend the concentrated stock solution with water at different proportions but 1:16, 1:100 and 1:200 are common ratios. The ratio listed indicates the amount of fertilizer concentrate taken up from the stock tank and the amount of final fertilizer solution that is made (after dilution). Therefore, for a 1:100 injection ration, 1 gallon (or 1 liter) of concentrated fertilizer stock solution is blended with water to produce 100 gallons (or 100 liters) of final fertilizer solution (1 part fertilizer concentrate + 99 parts water = 100 parts of diluted fertilizer).
There are various types of injectors. Some allow the greenhouse manager to set the injection ratio (i.e. Dosatrons) of concentrated fertilizer stock solution to water. Others injectors allow for a certain E.C. to be set and the appropriate amount of fertilizer stock solution mixed with water to achieve the desired E.C.
Hozon and Syfonex (sometimes referred to as Venturi injectors) injectors are small, brass units that screw onto a faucet at one end and onto a hose at the other end. When water passes through a restricted opening in the brass unit, a pressure differential between the waterline and the stock tank occurs. The suction pulls concentrated fertilizer solution from a tank or bucket into the brass unit from the suction line and mixes it with the clear water coming in through the faucet (thus creating a larger volume of diluted fertilizer flowing from the hose). These types of injectors are simple, inexpensive and can be easily attached to any faucet. They typically are designed to inject concentrated fertilizer at a 1:16 ratio. However, they do not provide constant control over the concentration being blended. This is because as fluctuations in water pressure occur, the suction in the brass unit changes and the amount of concentrated fertilizer taken up changes. A minimum of 35 pounds per square inch of constant water pressure has been recommended for these injectors to function properly. Additionally, back pressure (i.e. stepping on the hose or having a “kink” in the hose) can cause the unit to stop siphoning. Hozon and Syfonex injectors should not be more than 50 feet from the hose outlet (watering end of hose). Longer hose lengths can cause significant back pressure and affect the amount of concentrated fertilizer stock being injected. If more than 50 feet of hose is required, the injector (and buckets of concentrated fertilizer solution) may be connected between two sections of hose. Besides fertilizers, these types of injectors can be used to dispense insecticides, fungicides, and other water-soluble chemicals through a hose. However, care should be taken to insure that the mixing ratio that is occurring is correct
Dosatron, DosMatic, Anderson, Smith, and Gewa injectors (also referred to as positive displacement injectors), provide consistent injector ratios over variations in water pressure as long as the specified water flow rate for the specific device is maintained. A specific amount of fertilizer stock solution, determined by filling a specifically sized chamber, is injected into the incoming clear water, which also is measured by the unit. Thus, as with hozon and syfonex injectors, a specific amount of concentrated fertilizer solution is mixed with a specific amount of water to create a dilute fertilizer solution. The major concern with these types of injectors is that a minimum and maximum water flow rate, as specified for each device and model, must be maintained.
Dosatron injectors operate using water pressure as the power source. They are installed directly into the water supply line. Water drives the injector, which takes up the required amount of fertilizer concentrate directly from a stock tank. Inside the injector, the concentrated fertilizer solution is blended with the clear water and the diluted fertilizer solution then moves out and down through the hose or supply line to be applied to the crop. The amount of concentrate that is taken up and blended with water is controlled by and proportional to the volume of water entering the injector irrespective of variations in water pressure. There are various models of Dosatron injectors with required flow rates ranging from 7 to 264 gallons per minute and with injection ratios of 1:50 to 1:3000. Dosatron units may also be used to inject chemicals, including acids so long as the concentration of the acid does not exceed 5%. Higher concentrations of acids may be injected if the units have the proper internal components. The greenhouse manager should be sure to read the product information carefully to determine proper uses of each model of injector.
As in the case of Dosatron injectors, DosMatic injectors operate without electricity and use water pressure as their power source and are installed directly in the irrigation line. Also like a Dosatron injector, water drives the uptake of concentrated fertilizer stock solution and the concentrate is mixed with clear water to form a dilute fertilizer solution before it moves downstream to the crop. The amount of concentrate taken up and mixed with water is directly proportional to the volume of water entering the injector despite variations in water pressure. Maximum flow rates for DosMatic injectors range from less than 1 to 100 gallons per minute with injector ratios from 1:10 to 1:4000 depending on the model. The injection ratio can be adjusted while in use. Many DosMatic injectors allow for injection of most acids and disinfectant chemicals. Some models are specially designed for irrigation water pH adjustment. The greenhouse manager should be sure to read the product information carefully to determine proper uses of each model of injector.
Anderson injectors use positive displacement to inject the concentrated fertilizer solution into the waterline. The injector measures the water flow rate and injects the desired volume of concentrated chemical into the water line. The volume is proportioned by a flow-metered pump. Most of these injectors require electricity, but can operate using rechargeable battery packs or solar cells. However, the S-series Anderson injector does not require electricity. Injection accuracy is maintained over a wide range of water flow rates and pressure ranges. Injector ratios can be set from 1:80 to over than 1:200 depending on the specific model. The injector ratio can also be adjusted while in operation. Maximum water flow rates for this type of injector range from 0.75 to 3,000 gallons per minute at pressures ranging from 15 to 125 pounds per square inch. Anderson injectors can have from one to many separate injection heads that allow for the injection of multiple concentrated stock solutions. All models can handle a wide range of chemicals including acids. Models are available for stationary and portable uses. Various monitors and probes can be installed in-line on the outlet side of the injector for monitoring of pH and electrical conductivity of the fertilizer or chemical solution being supplied to the crops.
Smith injectors require no electricity to operate as they rely on water passing through a water motor to run the injector pump. The pump meters the volume of water running through the unit. The water causes a pump to revolve and a prescribed amount of fertilizer is injected for each revolution of the pump (for each stroke of the pump). The concentrated fertilizer solution to clear water remains the same regardless of changes in flow rates or water pressure. Smith injectors may be used to inject a variety of fertilizers and chemicals. Models are available that are specifically designed for acid injection and algaecide injection. Different models are designed to operate at different water flow rates and have different injection ratios that are factory set (cannot be adjusted by the greenhouse manager).
The Gewa injector is unique in that is has no suction or pumping device. Suspended inside of a steel tank is a plastic membrane or bladder. The concentrated fertilizer solution is placed inside of the bladder. When the water is turned on, it surrounds the membrane and applies pressure to the bladder which in turn forces a calibrated amount of concentrated fertilizer solution into the waterline. During operation, the bladder inside of the tank folds down on itself. Because the concentrated fertilizer solution has a higher specific weight than the clear water, folding-in takes place from the top down (fertilizer solution settles to bottom). Be sure the center tube inside of the bladder is in place during operation to prevent the membrane from sealing off the flow of solution. The only moving part in a Gewa injector is a float valve. This bronze, spring-loaded float value measures water flow on the inlet side of the valve and allows a specific amount of concentrated fertilizer solution to be injected. A sudden decrease in water pressure or water flow rate does not affect the proportioning of the valve. Various models of Gewa injectors are available and they come in sizes from 4- to 26-gallon capacity. Injection ratios range from 1:20 up to 1:300 and are accurate to within 4 percent. The thick steel tank makes up the bulk (and weight) of the Gewa injector. A water flow rate of 1.6 to 88 gallons per minute and water pressures up to 125 pounds per square inch are accommodated by this type of injector. Periodically, the inner membrane must be replaced, which requires disassembling the unit. Gewa injectors are most commonly used a portable injectors that may be placed on hand carts and moved around the greenhouse operation.
When choosing an injector, numerous factors should be considered. These factors include the size of the greenhouse operation, types of fertilizers or chemicals (including acids) that need to be injected, water flow rates available, water pressure available, minimum and maximum size of areas to be fertilized at a time, amount of fertilizer solution required to fertilize each greenhouse or zone, time required to deliver the required solution, quality of water to be used, portable versus stationary needs, maintenance requirements and cost of the injector. Always be sure to read the manufactures usage recommendations, specifications and maintenance recommendations for an injector.
Internal components of many injectors are made of stainless steel to resist corrosive fertilizers and other chemicals. If being used to inject acid, the injector selected must be equipped to handle acids. The type of acid to be injected and its concentration are important. Any internal parts of injectors to be used for sulfuric acid must be made of acid-resistant rubber, while for phosphoric acid injection these same parts may be made of stainless steel. If pesticides and insecticides are to be injected on a routine basis, the internal components of the injector should contain no plastic parts because many insecticides and fungicides contain a hydrocarbon base that may be harmful to PVC plastics.
It is often desirable to have the ability to inject several fertilizers (or other chemicals) at the same time that cannot be mixed together as concentrated solutions in the same stock tank. If certain components are mixed together in the same stock tank, they may form insoluble compounds that precipitate out of solution. In this situation, the incompatible fertilizers (or fertilizer salts) are kept in separate stock tanks and are injected directly into the irrigation stream with flowing water where their lower concentration and the water movement prevents precipitation. As a rule, sulfates should not be mixed with calcium in high concentrations (concentrated stock solutions) as the result is insoluble calcium sulfate (gypsum) and calcium phosphate. Phosphates should not be mixed with calcium or iron in high concentrations as insoluble calcium phosphate and iron phosphate result, respectively. Potassium bicarbonate should also not be mixed with other fertilizer salts as the resulting high pH may cause many fertilizer salts to precipitate out of solution. Because of these incompatibilities, multiple stock tanks and multiple injectors or injectors with multiple injection heads may be required.
The intake strainer and suction tube of the injector that leads into the fertilizer stock tanks should be positioned 2 to 3 inches above the bottom of the stock tank to avoid siphoning undissolved concentrated fertilizer salts. Be sure to periodically inspect the strainer on the suction tube to make sure it is not clogged. Finally, be sure to periodically test the injector to make sure that it is functioning correctly and injecting at the set ratio (see “Testing Fertilizer Injectors” in the “Mineral Nutrition” learning unit).
Stock tanks, holding tank and constructed lagoons
Stock tanks are used to prepare and store concentrated solutions (i.e. fertilizers) that can be blended with water using an injector to achieve a desired final concentration. The concentrated stock is usually injected directly into the water line where it is diluted and sent on to the crop. Other stock tanks may hold clear water used to irrigate or to dilute concentrated fertilizer solutions if required. Stock tank size depends on the injector ratio and daily water usage requirements. The stock tank should be large enough to allow the entire fertilization job to be completed with one batch of fertilizer concentrate. A larger stock tank is needed if a low injector ratio is used and if the injector is used frequently.
Stock tanks should be opaque since chelating agents in fertilizers used to keep micronutrients available to the plants break down if exposed to light. Stock tanks should be covered to prevent algae growth, to keep debris out of the stock tank and to minimize evaporation from the tank. Undissolved fertilizer salts can accumulate in the bottom of the stock tank, which results in large differences in fertilizer concentration. If a large stock tank is used, make sure that the fertilizer stock solution is well mixed using an agitator before use.
Holding tanks are generally used to store diluted fertilizer solutions that are immediately ready to be supplied to the crop (are at the desired concentration). The solution in the tank is usually pumped out to some type of closed recirculating irrigation system such as ebb-and-flow benches, Dutch trays or flood floors. These tanks need to have a capacity large enough to supply fertilizer to at least a complete greenhouse or irrigation zone in a greenhouse. After irrigation, the solution is typically filtered and returned to the holding tanks where it can be adjust if necessary and used to irrigate the next greenhouse or zone. As with stock tanks, holding tanks should be opaque to exclude light and covered.
In addition to tanks, water or fertilizer solutions may be stored in constructed storage lagoons lined with water impermeable liner and often covered with a light-excluding polypropylene cover. The cover blocks out light to prevent algal growth and keeps other types of debris from entering the irrigation system.
Filters
Irrigation water may contain contaminants (i.e. plant debris, algae, etc.) that can clog irrigation lines and emitters. To remove these materials and prevent clogging, the water is passed through a filter made of various types of wire mesh or paper, or through sand columns.
Solenoid valves
These devices are magnetic switches that control water flow. Solenoid valves can be connected to a timer or computer. When the timer or computer triggers an electric current and the electric current flows through the solenoid valve, it activates a magnet that in turn opens and allows water to flow.
Pressure regulators
Many emitters, drip tubes and drip tapes operate within certain water pressure ranges. The incoming water pressure is often higher than what the emitter, drip tube or drip tape is designed to handle. Excessive water pressures can break emitters or cause drip tapes to rupture. Therefore, pressure regulators are placed in the irrigation line to reduce water pressure to levels appropriate for the emitter, drip tubes or drip tapes being used.
Clocks/computer controls
Clocks or computerized controls are used to automatically control the frequency and timing of irrigation. These may be systems designed to control multiple greenhouses or zones in greenhouses or they may be mounted to specific irrigation devices such as is the case with individual controllers on irrigation booms.
Water meters
These devices measure the amount of water being used and are legally required in some states particularly where water use for agriculture is regulated.
Back-flow preventers
After liquid fertilization is terminated, suction in the water line may cause fertilizer solution to be pulled back into the water line resulting in fertilizer entering the potable water supply. To prevent this from occurring, back-flow preventers should be installed in the water line between the incoming water and the fertilizer injector.