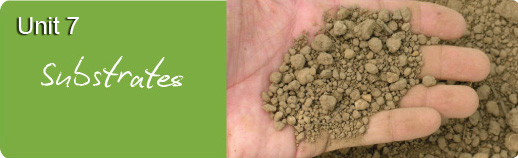
Section 4: Common Substrate Amendments
Lime and ground limestone
Substrates containing significant amounts of sphagnum peat or other acidic components usually require the addition of some type of lime or ground limestone to increase the substrate pH to a desirable level. Several types of pre-plant amendments may be used to increase substrate pH.
Hydrated lime [Ca(OH)2] is typically available as a fine powder and causes a rapid increase in substrate pH, but it has minimal residual effect on pH. Therefore, it is primarily used as a substrate amendment when a rapid pH adjustment is required. Where residual pH control is desired, hydrated lime must be used in combination with other slower-reacting components. Hydrated lime should be used with caution as large quantities can be caustic to plants. Furthermore, hydrated lime should be avoided where significant levels of urea or ammoniacal (NH4+) nitrogen have been included in the substrate as the rapid pH increase brought about may result in the evolution of phytotoxic ammonia (NH3) in the substrate.
Ground calcitic limestone (CaCO3) contains 36% - 39% calcium. It reacts more slowly in the substrate than hydrated lime, but it has a longer residual effect on substrate pH than hydrated lime. Dolomitic limestone (CaCO3*MgCO3) typically contains up to 12% magnesium depending on its specific chemical makeup. It is often preferred to calcitic limestone because in addition to increasing pH and providing a source of calcium, it provides magnesium.
When discussing the reaction of a lime or ground limestone in a substrate, there are three aspects of the reaction (and thus the pH increase) that are of interest. The first aspect is the reaction rate. This generally refers to how fast a limestone increases the pH of the substrate up to the point of equilibrium (where the pH no longer increases as a result of the lime or limestone). Another factor is at what pH does pH equilibrium occur. Finally, the residual effect of the limestone is important. This is essentially how much of a reservoir of calcium carbonate exists (once equilibrium has been reached) to maintain the pH in a desirable range, particularly if low alkalinity water and acidic fertilizers (which tend to push pH down over time) are used.
Many factors affect the specific reaction of a ground limestone when incorporated into a substrate. One factor is the grind size of the limestone. Ground limestone is classified based upon its particle size distribution. Pulverized limestone is classified as having a particle size that allows 60% of the particles to pass through a 100 mesh (150 µm) screen. A superfine limestone has a particle size that allows 60% of its particles to pass through a 200 mesh (75 µm) screen. Microfine limestone has a particle size that allows 95% of its particles to pass through a 325 mesh (45 µm) screen. The general conclusion from research that has been conducted on particle size was that the finer the particle size, the more rapid the reaction rate of a limestone. Likewise, the finer the particle size, the less residual effect of the limestone. More specifically, in research trials, a coarse particle with a size greater than 20 mesh (particle size of greater than 0.850 mm collected on a 20 mesh screen) was very slow to react and had little residual pH buffering capacity (ability to neutral acids over time and prevent pH decreased in the substrate). A limestone particle size of 20 - 100 mesh (particle size of less than 0.850 mm and larger than 0.150 mm) reacted and increased substrate pH and had a significant residual pH buffering capacity over the crop production period. A limestone particle size of 100 - 200 mesh (smaller than 0.150 mm and larger than 0.075 mm) was very reactive, rapidly increased pH levels to high levels and had little residual pH buffering capacity. Thus, the conclusion was that limestone with particle sizes within a 20 - 100 mesh range was best for greenhouse substrates.
The specific chemical makeup of the limestone and its hardness also affects its reaction rate. Typically, the harder the limestone, the slower the reaction rate and the greater its residual effect on the pH of the substrate.
In addition to grind size, chemical makeup and hardness of the limestone affecting the reaction of a limestone when added to a substrate, the substrate itself will have an important impact. Different substrates will have different initial pH and different cation-exchange-capacities which will result in different buffering capacities. Even sphagnum peat from different sources may have different initial pH and buffering capacities, and thus a given amount of limestone can result in different increases in pH with different peat types or sources.
Recommendations for the amount of a ground limestone to add to a substrate to achieve a desired pH vary. One recommendation for peat-based substrates was to incorporate 10 - 15 lbs of calcitic or dolomitic limestone per cubic yard with 2.5 to 3.0 lbs of ground calcitic or dolomitic resulting in approximately a 0.5 unit increase in pH. Another recommendation has been 8-10 lbs of dolomitic limestone per cubic yard for peat-based substrates and 5-6 lbs of dolomitic limestone per cubic yard for bark-based substrates. In published research trials, dolomitic limestone incorporated into a peat and perlite substrate at a rate of 3, 6, or 9 kg•m-3 increased the pH of the substrate from 3.9 to 5.8, 5.8 and 5.9, respectively. However, the residual activity varied based on the amount of limestone added. The pH of the substrate receiving only 3 kg•m-3 decreased over the next 16 weeks from 5.8. The pH of the substrate receiving 6 kg•m-3 increased to 6.0 by week 6 and then decreased during the following 10 weeks. The pH of the substrate receiving only 9 kg.m-3 increased to 6.2 after 6 weeks and then decreased to 6.0 for the remaining 10 weeks that the substrate was monitored. When a dolomitic hydrated limestone was incorporated at a rate of 0.9, 1.2 and 1.5 kg•m-3 into a 70% sphagnum peat and 30% perlite substrate, the pH increased to 5.0, 5.7 and 6.4, respectively, and remained relatively constant and those pH levels for 28 days.
Because of all of the factors that can affect the reaction of limestone when added to a substrate, it can be difficult to make specific recommendations regarding the amount of limestone to add to a substrate to achieve a specific pH. All of the studies that have been conducted on the effect of various limes and limestones on the pH of root substrates have used different substrates as well as different sources and types of lime and limestone. Although the rates discussed above serve as a general starting point or guide, greenhouse managers should experiment to determine exactly how a given amount of lime or limestone will affect the pH of the intended substrates. If substrates, substrate components, or limestone source is changed, evaluations with small test batches of substrate with varying amounts of limestone added should be conducted to determine what pH changes might occur. The greatest increase in pH usually occurs within the first two days of mixing. However, the pH will continue to increase and will equilibrate after 7 to 14 days. Therefore, it is generally recommended that the pH of the substrate be tested after 7 days. When conducting tests, it is important that the substrate be moist in order for the limestone to react and increase the pH.
Iron sulfate, aluminum sulfate and elemental sulfur
Because most greenhouse substrates are based on sphagnum peat which is acidic, it is most common that the pH of the substrate must be increased using lime or a ground limestone. However, in some cases components that have a pH that is higher than desired may be used to formulate a substrate. In these situations, iron sulfate, aluminum sulfate or elemental sulfur may be added as a pre-plant amendment to lower the pH of the substrate. Iron sulfate and aluminum sulfate are relatively quick acting but have minimal residual effect. Elemental sulfur is slow-reacting but has more residual effect on substrate pH. Elemental sulfur at a rate of 0.25 to 0.5 lbs•yd-3 or iron sulfate at 0.5 to 1.0 lbs•yd-3 were reported to lower substrate pH by 0.5 units. However, as with using limestone to increase pH, the reaction will vary depending on the specific substrate and the environmental conditions. Therefore, it is best to experiment to determine exactly how a given amount of a sulfur compound will affect the chemistry of the substrate.
Superphosphates
Superphosphate [Ca(H2PO4)*2H2O + CaSO4] or triple superphosphate [Ca(H2PO4)2*2H2O] are sometimes incorporated into the substrate as a pre-plant amendment as a phosphorus source. A typical superphosphate contains 7% to 9.5% phosphorus while a typical triple superphosphate contains 17% to 23% phosphorus. Both contain calcium and have been reported to contain varying amounts of boron, copper, manganese, molybdenum and zinc. A typical recommended rate of incorporation of superphosphate has been 4.5 lbs•yd-3 while 2.0 lbs•yd-3 has often been recommended for triple superphosphate. The actual desired incorporation rate will depend on the crop and the desired P concentration. Superphosphate and triple superphosphate have been reported to contain fluoride and for this reason it has often (although not universally agreed upon) been recommended that they not be included in substrates to be used to produce lilies, certain foliage plants or other monocotyledonous crops that are sensitive to fluoride. Reports regarding the effect of superphosphate and triple superphosphate on substrate pH have been contradictory. Superphosphate and triple superphosphate were reported by one researcher to have a neutral effect on substrate pH. However, other researchers reported that both superphosphate and triple superphosphate reduced the pH of a peat and sand substrate. The difference in these results may have been a function of the specific substrates used in the respective trials and the amount of sulfate in the substrate.
Superphosphate and triple superphosphate are no longer as commonly used as a substrate amendment as they once were used. There are two primary reasons for their reduced usage. The first is the increase in the use of complete water soluble fertilizers which are more often used as the sole phosphorus source. These fertilizers most often use ammonium phosphate or diammonium phosphate as the phosphorus source. The second was the discovery that high phosphorus levels resulted in elongation of young plants and thus greenhouse managers began to reduce phosphorus levels supplied to greenhouse crops.
Wetting agents
Wetting agents are a class of surfactants that are used to break surface tension and allow substrates to more readily absorb water. Wetting agents are particularly important for sphagnum peat-based substrates because dry sphagnum peat is very hydrophobic (repels water). Being surfactants, wetting agents varying significantly in their chemistry. Anionic surfactants tend to be used as foaming agents and not as wetting agents. Cationic surfactants are often highly toxic to plants. Most surfactants used as wetting agents for horticultural substrates tend to be nonionic. Many older wetting agents are based upon ethylene oxide polymers or propylene oxide polymers. Many newer wetting agents are polyoxyalkylene glycols. The later are less phytotoxic to plants than the ethylene oxide or propylene oxide polymers, but they also tend to be broken down by microbial activity faster and thus have a shorter life span than the ethylene oxide and propylene oxide polymers. Wetting agents are broken down over time by microbial activity and therefore their effectiveness diminishes over time. Researchers reported that a wetting agent added to a peat-based substrate lost only 30% of its effectiveness over a 40 week period. However, some commercial product labels caution that the wetting agent effectiveness will be reduced after 4 months. The exact life span of a given wetting agent will be determined by the specific chemistry of the wetting agent and the conditions under which the substrate is stored after the wetting agent is incorporated. Growers should consult with the manufacturer of a specific wetting agent to determine how long the wetting agent is effective after being blended into the substrate.
Wetting agents are available as liquids or as granular materials. Liquid formulations are generally blended with a specified amount of water and applied to the substrate while mixing to insure uniform distribution. Granular formulations which have the wetting agent applied to a carrier such as fine vermiculite also may be added to the substrate while mixing. The primary importance is to specifically follow the label for the specific wetting agent being used and to be sure to obtain uniformity when mixing.
Many wetting agents may also be applied as drenches to the substrate of a crop after planting and/or during production. This is particularly useful for long-term crops where the wetting agent may begin to loose its effectiveness before the crop production cycle is complete. Some wetting agents are designed to be included in liquid fertilization programs and therefore, the wetting agent may be applied periodically or with each irrigation. Typically, the more frequently the wetting agent is applied, the lower the rate that is used and product labels list the rate recommended for each use and application method. Greenhouse managers should check the product label to determine if the specific wetting agent may be applied as drenches to actively growing crops or through the fertilization program and, if so, at what rate and under what environmental conditions. Failure to specifically follow label recommendations can result in plant damage.
Although there are numerous wetting agents available, the three that are most commonly used in conjunction with substrates are Suffusion®, Soax®and Aquagro®. Suffusion® is available in liquid, granular and tablet forms. Soax® and Aquagro® are available in liquid and granular forms.
The primary function of a wetting agent is to reduce surface tension and allow the substrate to fully wet up and absorb water to its fullest potential. Wetting agents do not change the physical properties of the substrate per se. However, by allowing the substrate to fully wet up, they in essence increase the water-holding capacity by allowing the substrate to absorb more water than it might without a wetting agent. In other words, the wetting agent allows the substrate to reach its full water-holding potential. Wetting agents have also been reported to increase drainage and air-filled pore space of some substrates. The information to support this claim is very limited and the data reported does not show dramatic increases in drainage and air-filled pore space with the use of a wetting agent. However, because substrates expand when they absorb water, and as they expand total pore space increases, it is reasonable that some of the increase in total pore space might be air-filled pore space. Regardless, many benefits may be obtained through the incorporation of an approved wetting agent in horticultural substrates.
Biological amendments
There are numerous biological products that have been designed to be added to substrates for greenhouse crop production. These include such products as Rootshield, SoilGuard, Mycostop and Actino-Iron. The majority of these biological amendments are incorporated into the substrate to suppress soil-born diseases caused by organisms such as species of Pythium, Phytophtora and Thielaviopsis. Some of these biological agents are specific strains of species of bacteria such as Bacillus, Streptomyces or Pseudomonas. Others are fungi such as Trichoderma or Gliocladium. These beneficial organisms may suppress disease development in one or more ways. They might cause induced plant resistance, they might directly parasitize the disease-causing organism, they might compete for space or food sources important to the disease-causing organism or they might produce antibiotics that inhibit development or kill the disease-causing organism.
Significant evidence has been generated by private companies as well as by universities that support the efficacy of such biological amendments. However, there has also been significant research published that has raised doubts regarding the efficacy of such biological amendments. In fact, in a review in 2005, Daughtrey and Benson reported that incorporation of biological components was effective at reducing disease incidence less than 20% of the time.
In 2006, Hoitink and Lewandowski published a review article and clearly pointed out that many factors can affect the efficacy of biological components added to substrates. Some of these factors include the nature of the substrate, the environmental conditions, and the crop. Considering the information published, the best course of action for growers interested in such amendments is to experiment with them on a small scale to determine their efficacy under the specific growing conditions and with the specific crops being grown. When conducting trials, control groups without the biological components should be included so that the specific effect of the biological agent may be determined.
Micronutrients
In some production situations, a micronutrient fertilizer package may be incorporated into the substrate to supply the micronutrient needs of the crop. These may be mixtures of sulfate salts (i.e. iron sulfate, zinc sulfate, copper sulfate, etc.) that are water soluble and readily available for uptake by the plant such as in the case of Promax® or S.T.E.M®. Although readily available for uptake by the plant, these fertilizers supply micronutrients for a relatively short period of time; generally 6 to 8 weeks. This time span may be adequate for some crops, such as bedding plants, but not for other longer term crops. Other types of micronutrient fertilizers embed the microelements in very small pieces of glass (FTE No. 555®) and are known as fritted microelements. Still others embed the micronutrients on clay particles (Esmigran®). These types of micronutrient fertilizers slowly release the microelements into the substrate and thus have a longer life span. Newer formulations of micronutrient packages such as Micromax® and Micromax Plus® may also include the macronutrients calcium, magnesium, and/or phosphorus.
Nutrient starter charges
Numerous components may be added to a substrate before use in order to increase the level of one or more mineral nutrients. These are usually added at rates that are designed to provide a low level of initial fertility for the developing crop (until the liquid fertilization program can take effect) and not to provide the entire nutritional need of the crop. For this reason, such amendments are referred to as starter charges. Some of the most common materials added as nutrient starter charges include calcium sulfate which is designed to provide calcium without causing an increase in substrate pH such as occurs with the addition of lime or ground limestone. Magnesium sulfate may be added to provide magnesium. Calcium nitrate provides both calcium and nitrogen while potassium nitrate provides potassium and nitrogen. Ammonium nitrate and urea may be added to provide nitrogen. Commonly recommended rates for these starter charges are listed in Table 2. However, the exact concentration of a specific starter charge component will depend on the desired concentration, environmental conditions and the crop to be grown.

