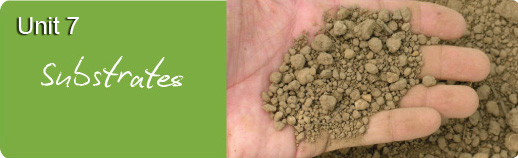
Section 7: Mixing and Handling of Growing Media
Selection of the appropriate components, the proper ratio of the components and the proper amendments are important first steps in designing a substrate that can be successfully used in the production of greenhouse crops. However, these decisions are only part of the process. Proper mixing and handling of the substrate can have a significant impact on the substrate's physical and chemical properties and its ultimate performance in the greenhouse. Even a well designed substrate may perform poorly if not mixed and handled properly.
Small batches of root substrate may be mixed by hand or by using a small-volume rotary drum mixer. If mixed by hand, the primary concern is that the substrate be thoroughly mixed and that any amendments are also evenly distributed throughout the substrate. Intermediate-volume batches of substrate may be mixed using a front end loader, rotary drum mixers, converted cement mixers or various types of automated mixing equipment. Where large volumes of substrate are required, they may be mixed as batches using large rotary mixers or mixers utilizing an auger apparatus that turns the components thereby mixing them. A continuous feed system may also be used. In this system, a series of hoppers containing substrate components and amendments are aligned over a conveyor belt. The materials are released onto the conveyor belt ("ribbon") that transports the materials. As the ribbon moves along, different components are placed one on top of the other until finally the components are dropped into a bin where an augur turns the products and transports the substrate to a temporary holding bin or directly to a pot-filling machine.
Substrate components should be mixed thoroughly. Otherwise, containers filled with a poorly mixed substrate may contain different combinations of components and amendments and the physical and chemical properties may vary among containers. Total pore space, air-filled pore space, drainage and water-holding capacities can vary significantly among containers if the root substrate is not uniform. Variations in these properties can result in some areas of the crop drying out more rapidly than other areas while some areas may remain wet for undesirably long periods of time. This uneven drying makes water management difficult. Areas that dry out too quickly may suffer water stress while areas that remain wet may serve as areas where soil-borne diseases are more likely to occur. Additionally, if amendments are not thoroughly mixed, the resulting chemical properties of the substrate may vary among containers. For example, if the lime is not evenly distributed throughout the substrate, the pH will vary among containers. Some may have unacceptably high pH while others may have a low pH.
Although uniform mixing is critical, the substrate should not be over-mixed. This is because as the substrate is turned or tumbled, the particles may be broken down. This creates smaller particle (i.e. "fines") sizes. These smaller particles result in a higher bulk density, reduced total pore space and reduced air-filled pore space. Therefore, although high quality components were selected and mixed at the appropriate ratios, the excessive mixing changed the physical properties of the components and the resulting substrate. No absolute rule can be provided regarding the amount of time required for proper mixing of a substrate. However, the goal is to mix only as much as is required to produce a uniform product.
Water should be added to the substrate during mixing. Water allows the substrate components to expand, thus maximizing the volume of the substrate and its total pore space. If the substrate is placed into containers in a dry condition and then watered, the substrate will not expand to its full potential. Furthermore, when water is added to a dry substrate in a container, the surface may appear wet, but the water will often channel through the substrate and out of the container. The substrate may appear to be wet on the surface, but may be dry below the surface of the container. It may make take many irrigation cycles to wet up the entire volume of the substrate and usually the substrate will never expand in volume to its full potential. In addition to its effect on the physical properties of a substrate, water is required for many amendments such a lime to begin to react when incorporated into the substrate.
Substrate that has been in compressed bales must be broken apart and fluffed to maximize the volume before it is placed into pots, flats, or plug trays. This is best accomplished using a bale buster and then fluffing the mix using a falling or tumbling motion (preferably over a ½" hardware cloth). Loose-fill substrate that has become compressed in bags due to shipping and storage may also need to be fluffed before use. Be careful not to over mix the substrate.
If not used immediately, the substrate should be stored moist and in a clean location. If the substrate is not in sealed bags or totes, it should be placed in bins, hoppers or other clean storage containers and not on bare ground or unclean surfaces in order to avoid contamination of the substrate with potentially harmful pathogenic bacteria or fungi or weed seeds. Ideally, the substrate should be covered to prevent contamination and to minimize moisture loss. If containers are pre-filled with substrate, they should not be allowed to dry out before use. Otherwise, rewetting may be a problem when plants are finally planted into the containers. Additionally, if containers are filled with substrate for later use, the containers should not be stacked on top of one another in such as way that the container weight is supported by the substrate. The weight of the containers and substrate compresses the substrate. This compression increases bulk density while reducing total pore space and air-filled pore space. Additionally, in a stack of containers or flats, not all of the containers are compressed equally. Therefore, in addition to compacting the substrate, a significant level of variability in the physical properties can be introduced and this, as with uneven mixing, may result in significant variability in the rate of drying once placed in the greenhouse. If containers or flats are stacked, containers should be staggered or boards used to separate layers of containers so that the weight is supported by the containers and not the substrate. If not used soon after filling, the stacks of substrate-filled pots should also be covered with plastic to minimize water loss and contamination.
Many greenhouse managers choose to purchase pre-mixed substrates that are ready for use. This option allows greenhouse managers to avoid the need for mixing equipment, reduces the required storage space and eliminates the time and expertise needed to appropriately mix the substrates. There are numerous commercial substrates on the market from which greenhouse managers may choose based upon their specific desired properties. If large enough volumes are required, custom-blended substrates may be ordered. Substrates may be purchased in small 2.8 cubic foot bags, loose bails, large totes or when very large volumes are required, substrates may be provided loose in semi-trucks that may be used to feed container-filling lines using an augur system.
As previously discussed, wetting agents improve the wettability of substrates. Most commercial mixes contain a wetting agent. However, wetting agents are broken down over time by microbial activity. The lifespan of a wetting agent depends upon the specific wetting agents and the storage conditions of the substrate. Greenhouse managers should be careful when using old substrate as the wetting agent activity may be greatly reduced over time and the substrate difficult to wet. Additionally when growing long-term crops, a maintenance application (applied as a substrate drench or through the irrigation system) of wetting agent might be necessary.
Substrates containing organic materials such as sphagnum peat and composted bark generally should not be pasteurized. This is because pasteurization will eliminate or reduce the populations of beneficial microorganisms. Where sand or field soils are being added to a substrate, and there is concern that disease organisms might be introduced into the substrate, it is preferable to pasteurize the mineral component and then add it to the organic components. Components such as perlite, vermiculite and PBH do not require pasteurization because they are exposed to sterilizing temperatures during production. When pasteurization is required for field soils or sand, the temperature of the material should be increased to 160°F (throughout the volume of material) for 30 minutes and then allowed to cool before use.
Get the Flash Player to see this video.
|
Get the Flash Player to see this video.
|
You are now at the end of Unit 7: Substrates. Click here to take the self-exam.
Your test results will be sent to Dr. Evans.
